RETHINK
The “RETHINK” project funded by the German Federal Ministry of Education & Research (BMBF) focused on sustainability, resource conservation and independence from supply bottlenecks. Together with the Institute for Machine Tools & Industrial Management (iwb) of the Technical University of Munich, our sister company ITQ and the water meter producer Lorenz, we advanced remanufacturing for the industrial circular economy in SMEs using existing systems. Industrial remanufacturing and the reuse of old parts will reduce environmental pollution and save up to 80% of raw materials. Production-threatening dependency on suppliers, as was evident in the initial lockdown of the pandemic, can be mitigated and become less important. A topic with future, actuality and great potential! The research partners set themselves the goal of developing a standardized procedure model for evaluating the systems in place in SMEs. The model provides entrepreneurs with a simple way of assessing which systems used to date can continue to be used for remanufacturing in production. This knowledge makes it easier to decide in favor of sustainability.
The project is was carried out by the Projektträger Karlsruhe (PTKA) of Karlsruhe Institute of Technology (KIT) and run until the end of August 2023.
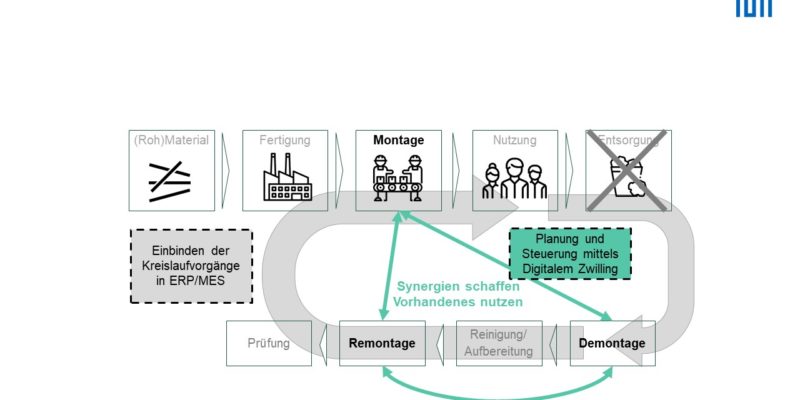
MC-SANDWICH
The “MC-Sandwich” project, funded by the Bavarian Research Foundation, dealed with the resource-conserving design of components, which is becoming increasingly important nowadays. Lightweight structures such as sandwich composites are an optimal solution for this. However, due to the difficult imaging of the curved surfaces, they are only used to a limited extent by the shaping core structure.
In the research project “MC-Sandwich” the aim was to realize complex, curved, metallic core structures with low density. 3D printing technologies are combined with carbon fiber reinforced plastic (CFRP). In order to integrate software development into the product portfolio and compatibility with Creo, the Software Factory‘s job was to create a digital component analysis and a pre-definition of critical wall thicknesses and distances.
In addition to Software Factory, the Fraunhofer IGCV, MT Aerospace AC, Schmelzmetall Deutschland GmbH, Hyperganic Technologies AG, Gierl DCP, EOS GmbH and Kuhn Beschichtung GmbH were the other partners working on the 2.5-year project.
REGULUS
In the REGULUS research project, iwb, with the help of the Software Factory, AMAG components Deutschland GmbH, Heggemann, FAU, Fronius Deutschland GmbH and Boeing Deutschland GmbH was developing a process chain consisting of additive and machining manufacturing processes for the resource-efficient production of large-volume aerospace structural components made of titanium alloys. The motivation for this project was based on the increasing use of hard-to-cut materials in aviation, which presents a particular challenge in the production of large-volume structural components. Due to the materials being difficult to cut, over 85% of the materials were wasted, leading to high production costs.
Based on this need to develop and implement a process chain for saving resources during production, arc-based additive production of raw contours was created. By utilizing this method, the material use is projected to be reduced by 90%.
The REGULUS project was funded by the Federal Ministry for Economic Affairs and Energy (BMWi) and managed by the German Aerospace Center e.V.
ReDiMon
Our last successful research project!
The goal of the project “Realistic digital models for assembly plants” (ReDiMon) was to map the current state of production plants transparently. Funded by the bayerische Verbundforschungsprogramm, we could advance this project together with the Institute for Machine Tools and Industrial Management of the Technical University of Munich (iwb), as well as the companies Conti Temic microelectronic and mts Consulting.
Digital models are usually created during the planning of a plant, but are often not regularly updated afterwards for cost reasons. During operation, they no longer represent the real condition correctly modified due to changes and wear.
The adaptation of the model should therefore be automated to a large extent. For this purpose, the model was continuously compared and updated with the process data evaluated by artificial intelligence, as well as with a 3D capture of the actual plant configuration.
This allows now more informed decisions to be made regarding maintenance, troubleshooting or reconfiguration. Undesirable downtimes of the production plant, but also the planning effort are minimized.
Link4Pro
Companies are faced with the challenge of making their operational procedures, processes and their intralogistic connections efficient. The existing value creation chains as well as their production facilities offer potential for increasing efficiency, as the system parameters and operating conditions are predominantly non-transparent.
The research project, Link4Pro, aimed to develop a system which connects facilities in a flexible manner. In order to do so, a combination of existing and unused data sources were utilized. The data were analyzed by modern techniques and artificial intelligence, thus weaknesses and unused potential are identified quickly and precisely. Through this flexible connection, companies will have the possibility to improve their own production process with minimal effort; consequently increasing productivity in a long-lasting way.
The consortium consisted of system developers, component manufacturers, system integrators and production companies which have production processes with multiple stages. The research project was lead by the Fraunhofer Institute for Manufacturing Engineering and Automation. In addition to Software Factory, 10 other partners from manufacturing and research backgrounds were working on developing a technical and economical solution, which evaluates manufacturing practice in line with pilot implementations, ultimately guaranteeing the transfer of the project results.
VIPER
Predictive maintenance and online process optimization of processing machines
The aim of the VIPER research project was to revolutionize online process optimization and predictive maintenance for complex processing machines. On the basis of machine data collected by sensors, the status of the machines is to be monitored and necessary action steps automatically triggered. In the future, it should also be possible for the machines involved to independently trigger an optimization of the process parameters. AI makes this possible! Software Factory took on the part of data analysis in this highly exciting project – using the IIoT platform ThingWorx and the analysis tool ThingWorx Analytics. The project was managed by the VDI/VDE. It was supported by the Bavarian State Ministry of Economics, Energy and Media. In addition to Software Factory, other well-known project partners such as the Fraunhofer IGCV, ITQ GmbH, AMPACK GmbH (Syntegon, formerly Bosch Packaging Technology) and HOSOKAWA ALPINE AG were involved in VIPER.
ProMoA
ProMoA was a project devoted to process and model-based automatic system development. The aim of the ProMoA joint project was to develop new methods and IT tools for the automatic, product-based planning of new systems and the simulation-based examination of the suitability and conversion of legacy systems. This planning system is also intended to take account of the impact of product design changes on system configurations. This will now permit the optimized and practically fully automated planning not only of completely new systems but also of required modifications to existing systems while simultaneously reducing the effort involved.
A number of other well-known companies were working together with Software Factory in that project. It was funded by the Federal Ministry of Education and Research (BMBF) and supported by the project sponsor Karlsruhe Research Center (PTKA).
EU INCLUSIVE
Modern manufacturing systems are becoming increasingly complex as a result of the growing demand for high productions rates with a consistently high level of quality and flexibility, i.e. the ability of production systems to adapt to constantly changing market requirements. Despite the high level of automation of machines and robots, human beings continue to be at the heart of the manufacturing workflow because it is they who monitor and supervise production. Human operators interact with machines and robots via human-machine interfaces (HMIs) that are unavoidably becoming more and more complex as new functions comprising many different operating modes and work instructions are implemented in production systems. In such scenarios, operators are confronted with many obstacles to efficient interaction with their machines. This is particularly true of middle-aged workers who feel ill at ease when interacting with complex computer systems, as well as of young, inexperienced or disabled individuals who are unable to operate this type of complex production system efficiently.
The aim of the INCLUSIVE project is to close the widening gap between machine complexity and the capabilities of users by developing an intelligent, innovative HMI that takes account of the user’s abilities and ensures the required flexibility by compensating for the operator’s limitations (e.g. resulting from age or lack of experience) while also taking advantage of their experience.
To achieve this, the developed HMI system must first be able to measure the cognitive load that is acceptable for the worker in question and their ability to cope with the automation tasks involved in interaction with the production system. It must also be able to adapt the automation functions and the volume of information in the production system to the measured capabilities of the user. In addition, the HMI must support less able users and train them appropriately to perform complex automation tasks. One way to achieve this is for the solution to include a virtual environment and an industrial social network.
The aim of the project was to ensure the highest possible level acceptance among workers by creating an inclusive working environment and to guarantee the productivity of new automated production systems. As part of this 36-month EU project, Software Factory was working closely together with 10 partners (universities and companies in the industrial and software development fields) throughout Europe.
Find out more about the success of the research project in a series of exciting videos, from interviews to demo cases.
FORobotics
Today, robots are usually used stationary, e.g. in production lines, due to the common construction of the robots. With research being done on mobile and team robotics, many more use-cases are possible in the future. Robots don’t have to be seen as replacement for human workers anymore then, but as partners, for instance as autonomously driving robots in factories.
Software Factory was part of the research group FORobotics, which focused on this topic and researches ad-hoc cooperating teams of robots. The project was aiming for solutions on examplary tasks from production environments. These tasks are supposed to be solved by teams of human workers and robots as well as by cooperating teams of robots. As an effect of the cooperation, value-creating time is planned to be increased, e.g. by the robot’s ability to multitask. The aim of the project was set to be reached by creating concepts for working in teams as well as by setting standards for interfaces and platforms, especially industrial standards like OPC UA. The work of our research group was furthermore accompanied by a parallel user evaluation. The projectpartners next to Software Factory: AREVA GmbH, Bertrandt GmbH, Fraunhofer IGCV, FAU Erlangen-Nürnberg, HEFTER Maschinenbau GmbH&Co. KG, ITQ GmbH, MAN Truck&Bus AG, Mangelberger GmbH, Mayser GmbH &Co KG, Metrilus GmbH, MRK Systeme GmbH, SALT Solutions GmbH, software4production GmbH, Stäubli Tec-Systems GmbH, Teamware GmbH, TU München, Universität Augsburg, Universität Bayreuth, Universität der Bundeswehr München and Yaskawa Europe GmbH.
ViWiAC
The ViWiAC research project was predominantly concerned with the visualization of the active structure connection in CAD.
The modelling tool had the task of visualizing the functionality in CAD in the form of active structures, which were already in the design of the system. Thus, the functions as well as the prerequisites for the design were traceable and comprehensive from the very beginning. After the implementation of the construction in CAD, a directly-linked visualization of the functions and designs on the CAD interface was offered for the first time. Modelling the function-design relationship according to the C & C²-A (contact and channel approach) was based on interactions while the product was in use.
The result was a significant simplification of being able to analyse the active structures, ultimately answering the question, “Why does it look the way it is?”
The 24-month project was funded by the Federal Ministry for Economic Affairs and Energy (BMWi) and supported by AiF Projekt GmbH ZIM cooperation projects. Software Factory worked on the project together with the Institute for Product Development (KIT IPEK) at the Karlsruhe Institute of Technology.
The aim of the project was to document the nominal functions of the system design. As a consequence, the analysis of the active structures was remarkably more manageable.
CICS
The CICS project on the “Potential, structure and interfaces of cloud-based industrial control services” was launched in 2014. The partners were the Düsseldorf-based Telelabor, a facility operated by the Competence Center Automation Düsseldorf (CCAD), and the Chair for Communication Systems at the University of Augsburg in cooperation with the Fraunhofer ESK in Munich. Also assisting in the project were Software Factory as well as other companies from the automation industry. The research project was funded by the BMWi (German Federal Ministry for Economic Affairs and Energy) via the electronic engineering research association at ZVEI e.V.
The aim of CICS was to develop a reference architecture based on web technologies that is suitable for the realization of control programs in the form of control services (in accordance with standard IEC 61131). This comprises rapid, reliable and secure process data interfaces (web connectors) and the use of the web protocols HTTP2, WebSocket and WebRTC. The control services use available public and/or private cloud structures for the management and implementation of CICS. An additional variant was to execute the control services on web clients (web browsers).
Among other things, the research results are making it possible to develop new, end-to-end, web-oriented control systems that can be adapted exceptionally flexibly and easily to meet application-specific requirements.
APOLI
The aim of the APOLI research project is to ensure greater security in business processes in the age of Industry 4.0. Focus is placed on the application-friendly authentication and authorization of the persons and objects involved in IT-assisted business processes. Running until the end of 2017, this project will develop optimally automated authentication and authorization procedures for industry, commerce, banks and services.
To this end, the researchers and engineers were evaluating the potential of the new technological approaches that have been the subject of such intense discussion: SDN (software defined networking) and NFV (network functions virtualization). Within the project, the Fraunhofer ESK was responsible for evaluating SDN and NFV. As an expert in the field of Industry 4.0 and the development of customized, requirements-oriented software solutions, Software Factory GmbH was the project partner responsible for machine integration in the solution using SDN and NFV. In addition, Software Factory was contributing its technical and methodological expertise in the field of application lifecycle management (ALM) through the provision of an ALM platform. Another partner in the project was Otto Bihler Maschinenfabrik Gmbh & Co KG. This company was accompanying the APOLI development process, providing the test environment for the machine connections and performing practical remote maintenance tests.
Sustain Grid
Software Factory was working together closely with its project partners Beckhoff Automation and Fraunhofer AISEC in the “Sustain Grid” research project, which was funded by the Bavarian State Ministry for Economic Affairs and Media, Energy and Technology.
The aim of the project was to rise to the challenges of the energy transition, which will demand a power supply infrastructure that is fit for the future.
One problem of renewable energies is the very high level of supply volatility. Transmission capacities are playing an increasingly important role in preventing critical supply situations from arising. Modern power electronics could cushion such risks. However, this requires that the key players in the sector coordinate their activities. This makes it necessary to resolve the contradiction between the need for a comprehensive flow of information, on the one hand, and the protection of data and system security, on the other.
Standardized, secure communication within the network is one of the most important prerequisites for the implementation of a reliable smart grid. The object of research was the security and conformity of the grid elements. One aspect of the research assignment was to develop suitable testing tools that permit reliable, long-term system integration, to identify the existing gaps in the field of testing and to remedy these shortfalls in smart grids by developing suitable test tools for the areas of communication and IT security. The focal points in this endeavor were interoperability tests for control devices in accordance with IEC 61850, conformity tests of inverters for the integration of PV systems in the low-voltage grid, testing in the smart metering field, and penetration tests for IT security in the grid.